|
gazza_no7
|
posted on 31st May 12 at 22:38 |
looks cool as f**k :D bet they are ace to race on!
|
Matty W
|
posted on 30th May 12 at 22:34 |
Not reaaly been on cs for a while.
Heres a few photos from the first race meet about a month back.
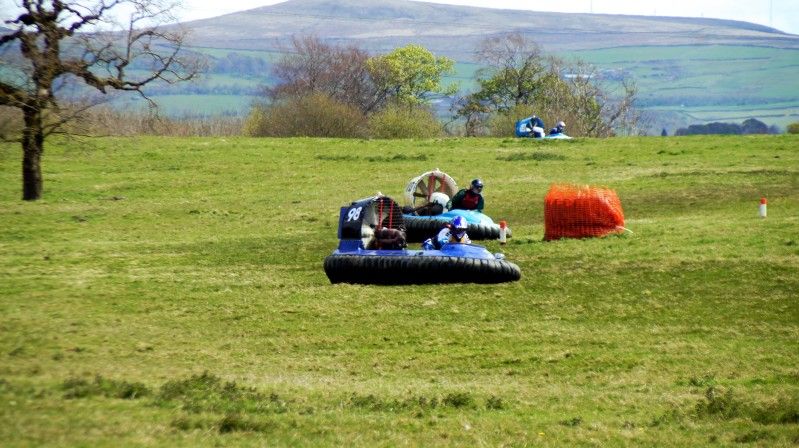
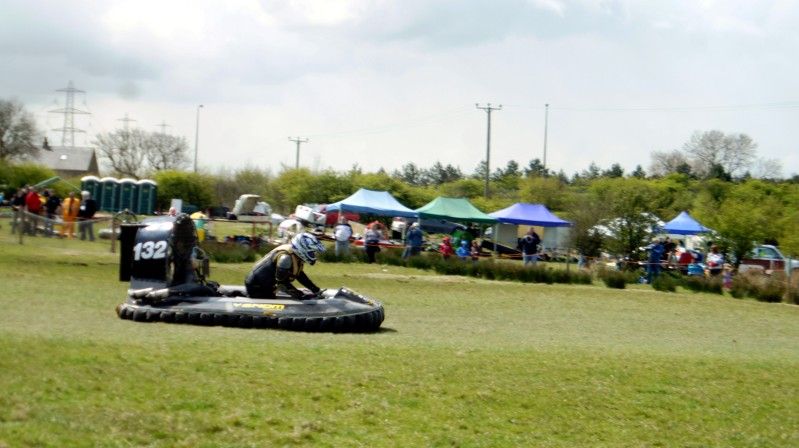

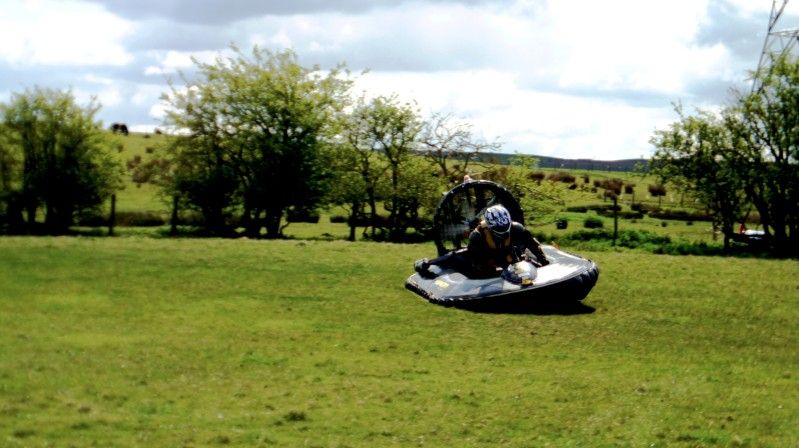
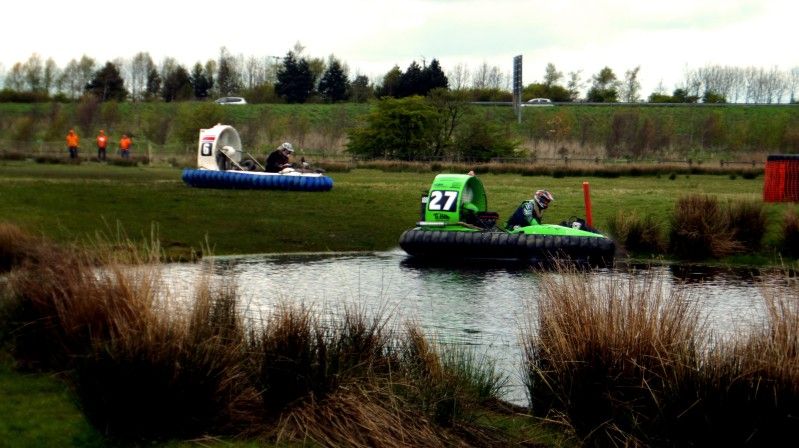
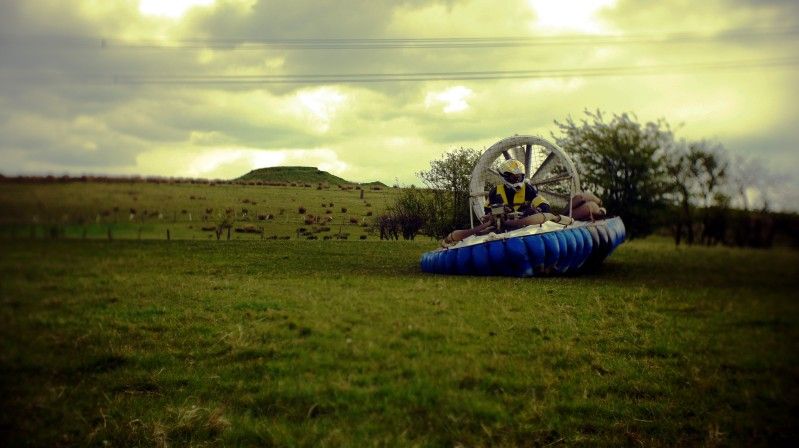
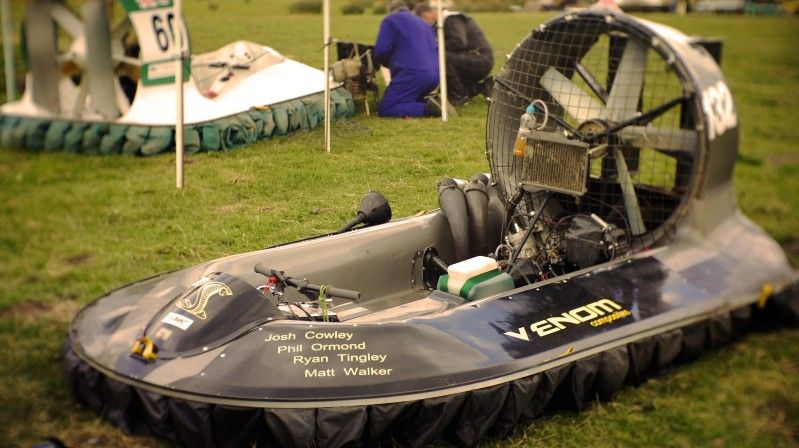
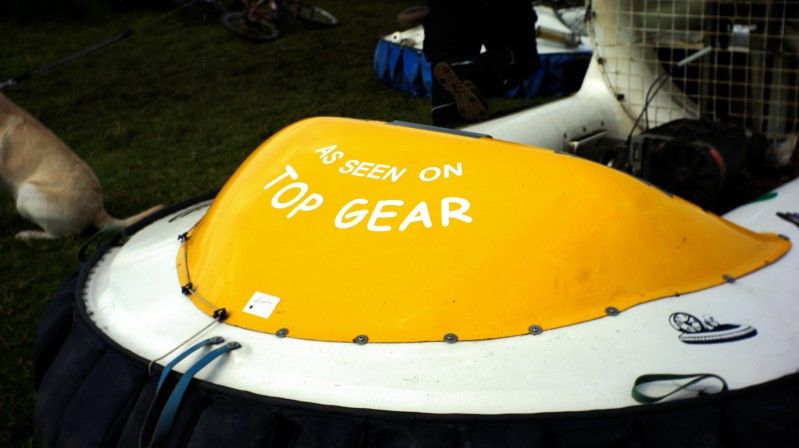
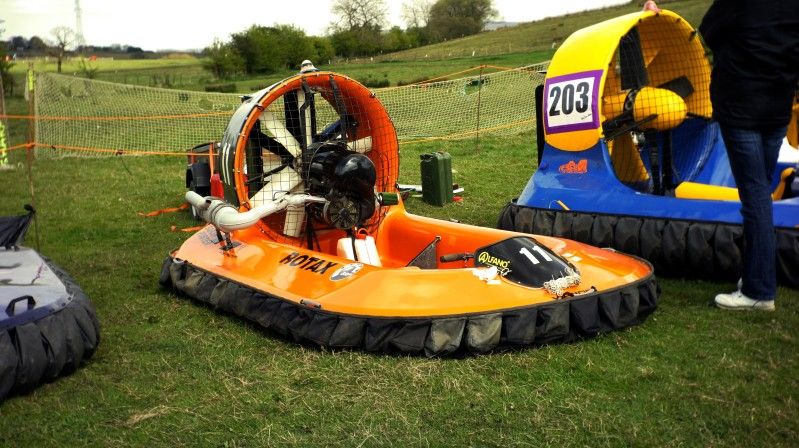
|
Matty W
|
posted on 30th Apr 12 at 00:06 |
the 12 craft has been put on hold for a few weeks due to prep of the 11 for the start of racing season. it crept up pretty quick so its all been a bit of a last minute rush. fortunatly there wasnt too much needed doing.
its had:
5 new blades
re-wired electronics
coolant flush
skimmed hub shaft so bearing fits tighter
re-welded fan guard
new steering cable
new handle bar mounting point
new grips
new drag handles
new fuel lines and non return breather valve
brace bar from fan frame to floor infront of the engine ( not in picture )
new duct cover
and repair patch to the left hand side.
still needs a new finger skirt and a couple of holes patching.
Before work:
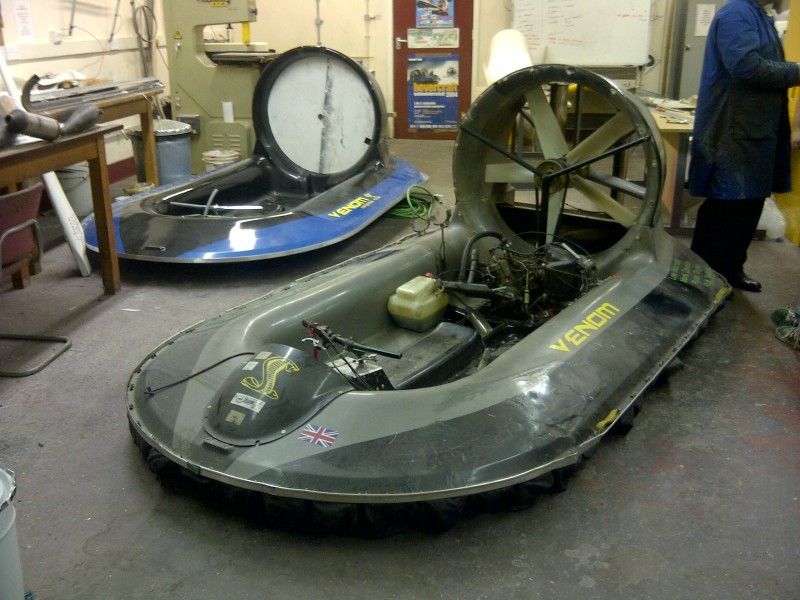
After some repair work:
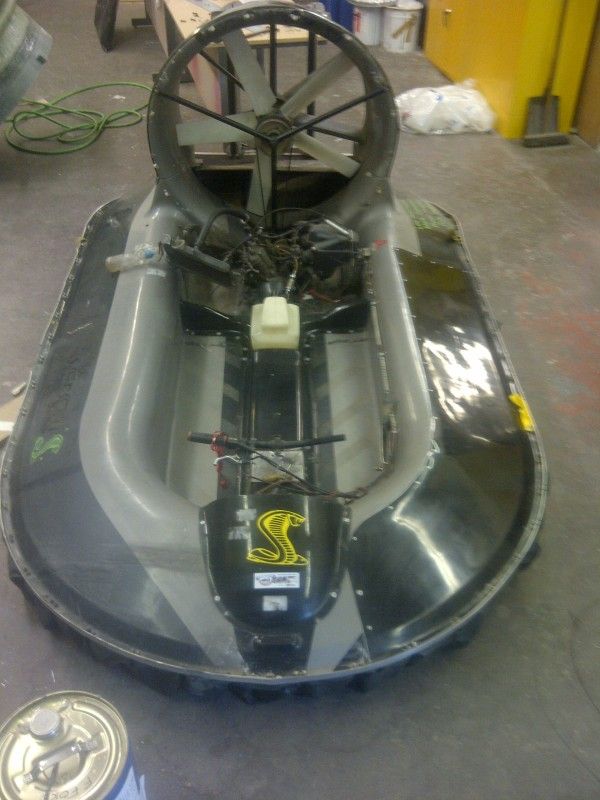
Testing again on tuesday
[Edited on 30-04-2012 by Matty W]
|
Matty W
|
posted on 15th Apr 12 at 18:00 |
Its like riding a 60mph bar of soap :lol:
|
nibnob21
|
posted on 15th Apr 12 at 17:58 |
Ha awesome, must be so much fun!
|
Matty W
|
posted on 15th Apr 12 at 17:49 |
Been away from uni for 2 weeks so no real update on the 2012 craft apart from the re-mapable ecu has turned up so we're going to get that set up with a ford edis coilpack and program a map for the Rotax 493
In the meantime ive been working with tony producing body panels for juno.
this is a side pod from a juno formula ford
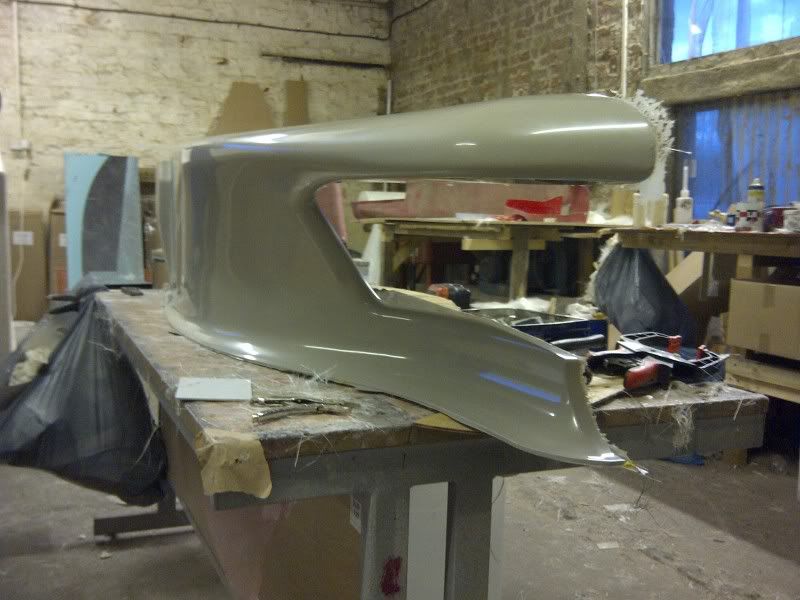
we've also done some testing of the 2011 craft in prep for the race season in 3 weeks.
theres a short video of it here
http://www.youtube.com/watch?v=q38rHrdCk50&context=C4f20c41ADvjVQa1PpcFO4Qx9MDeLcoD7d-yPoQ5AoZIr9ZysN714=
[Edited on 29-04-2012 by Matty W]
|
Matty W
|
posted on 31st Mar 12 at 10:38 |
No m8. not scene enough
|
Steve
|
posted on 31st Mar 12 at 08:35 |
This is nice r u taking it to the ring
|
Matty W
|
posted on 31st Mar 12 at 06:31 |
Glassed in the duct support. no flex now where the blade runs.
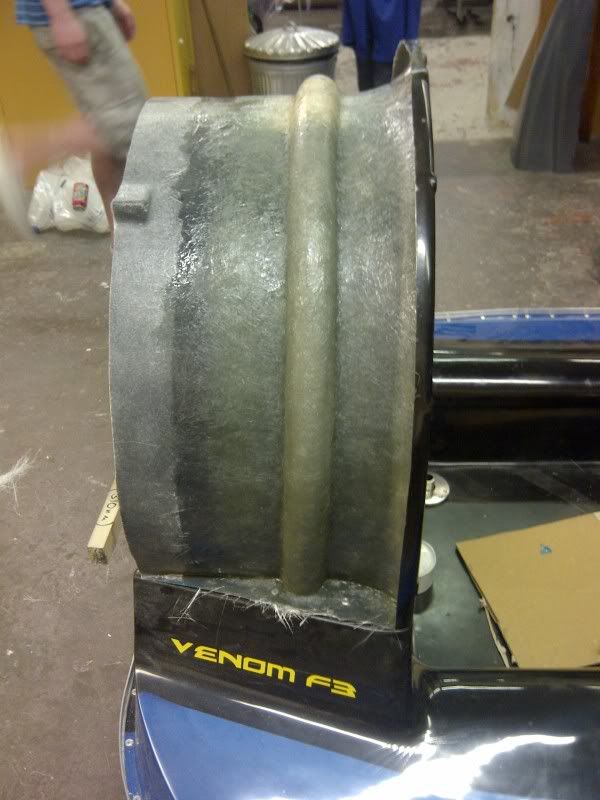
These ally blocks will be machined out to hold the bearings for the driveshaft. the fan frame will also mount to the top
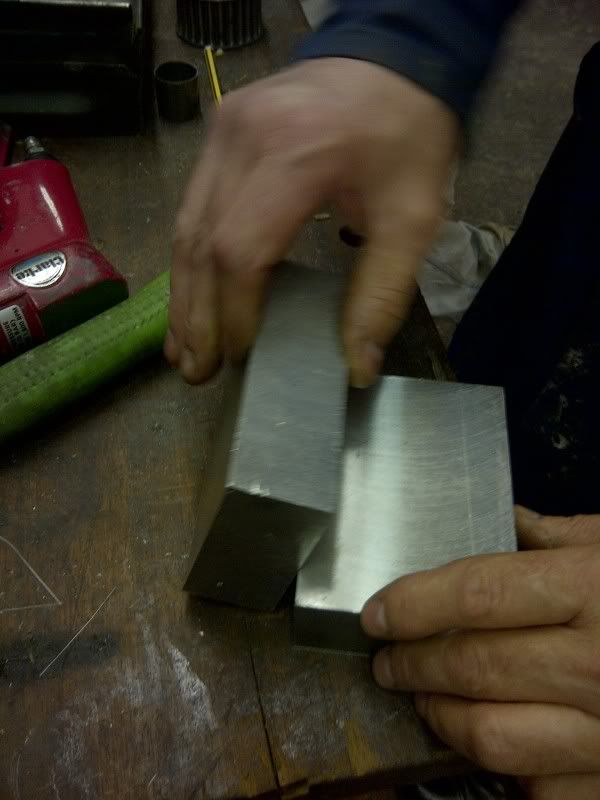
And working through some equations to get the correct pulley ratio for maximum tip speed at peak power

|
corsadonk
|
posted on 16th Mar 12 at 19:32 |
It's looks really modern, not like the ones I've seen in the past. :cool:
|
Matty W
|
posted on 16th Mar 12 at 18:32 |
got some photos of the work.
Rear bump strip in place and riveted together
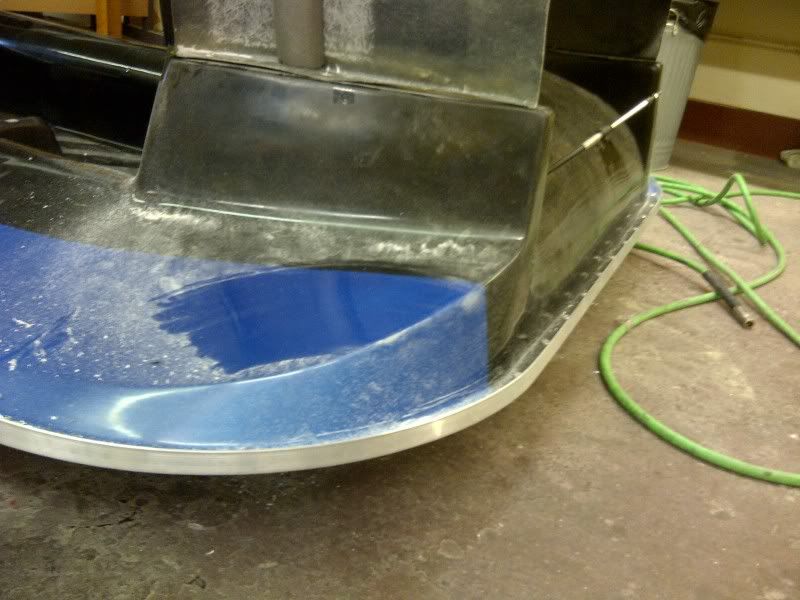
The lip inside the duct has to be nearly flush as the blade clearance is only a few milimeters

The round disc will keep the shape of the duct whilst we glass the re-enfocement into place. the peice of wood at the back of the duct is to stop it falling forward and twatting the hull
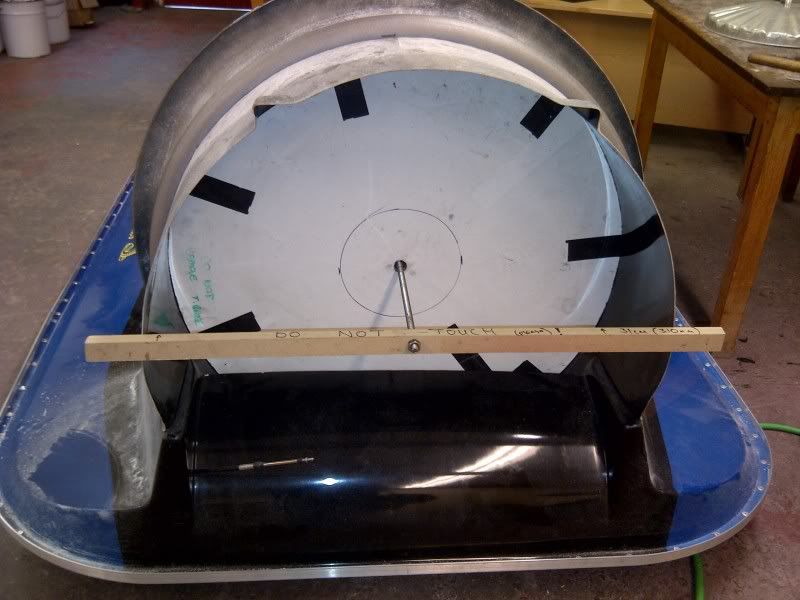
this pipe insulation will be glassed over with 4 layers and will help hold the shape. It is regulation to have a re-enforced area 100mm either side of where the blades sit in the duct incase of a blade off
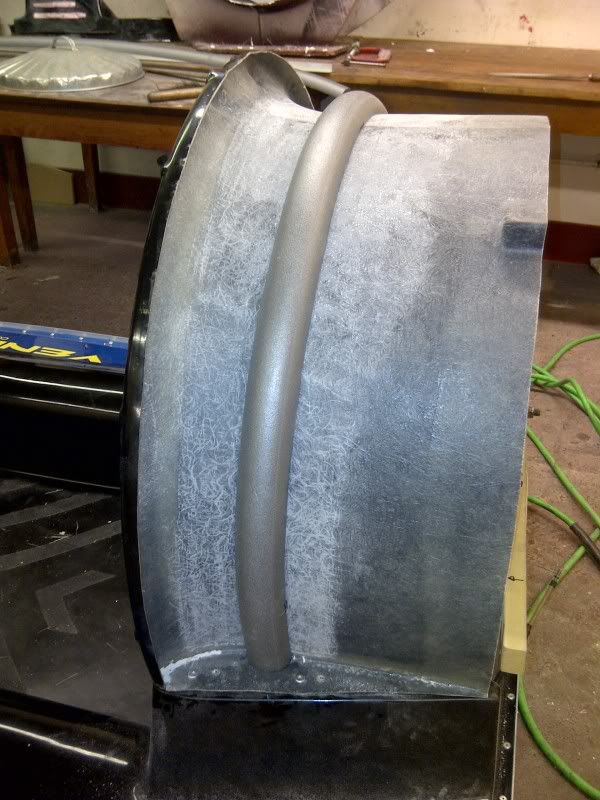
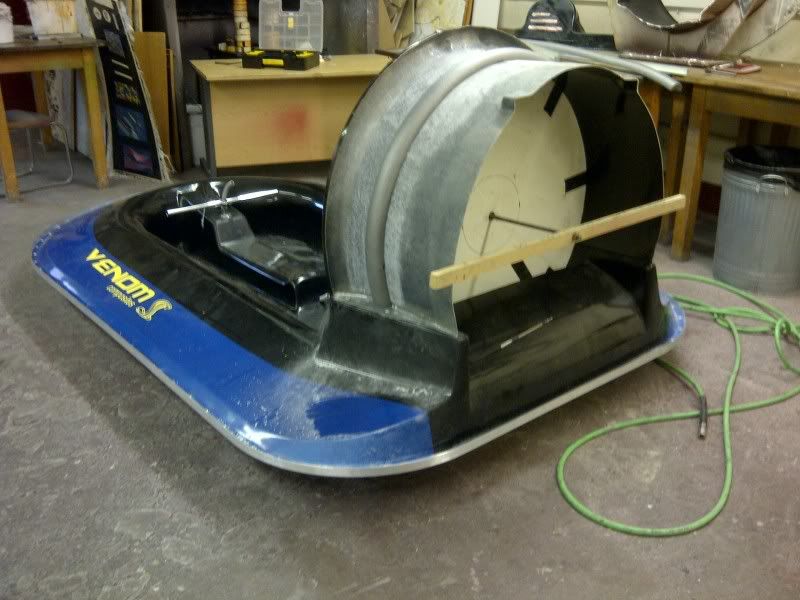
also made a repair pannel for the 2011 hull after it took some smashes last season.
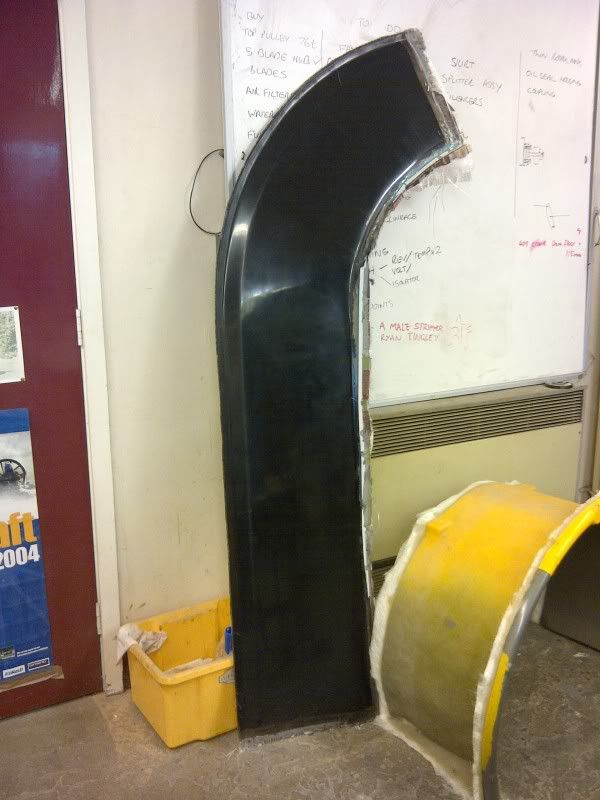
12 blade hub with 6 blades
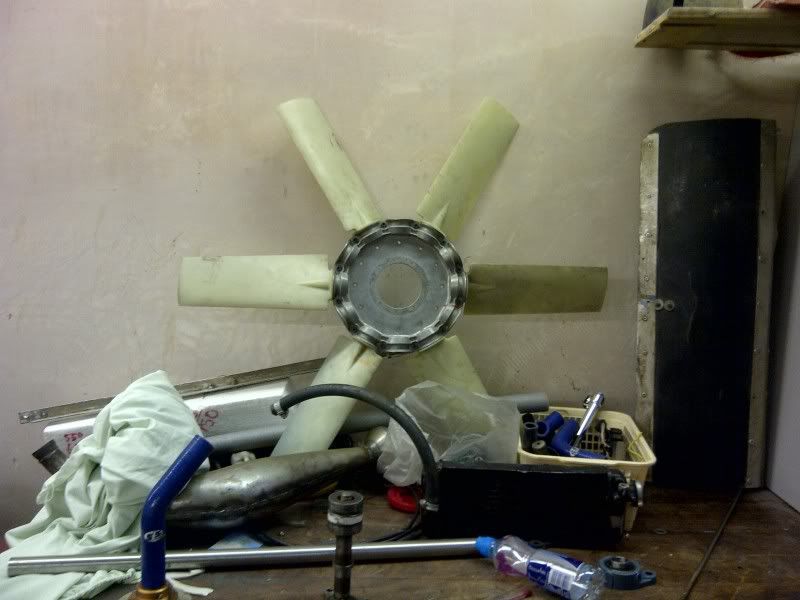
The beginings of the footplate mould
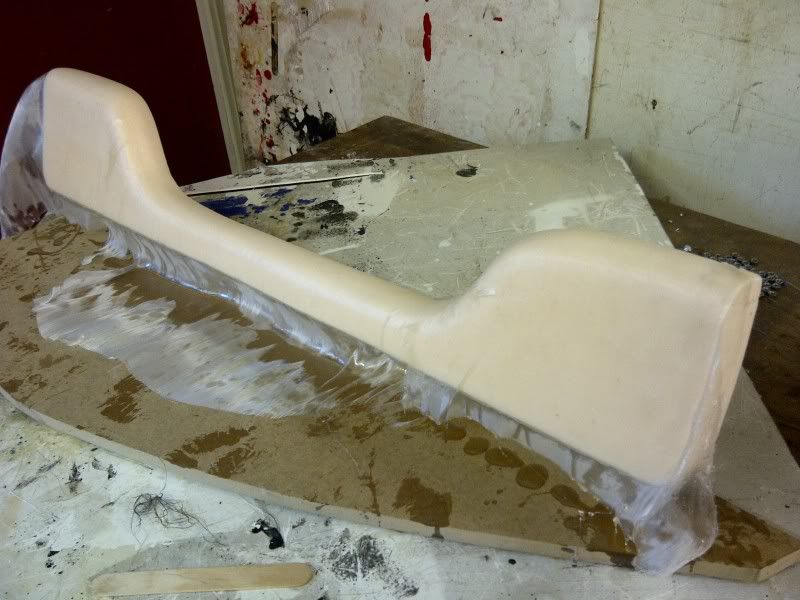
|
Matty W
|
posted on 13th Mar 12 at 22:30 |
Small update: back end of the craft now has its aluminum edging around it and the whole craft is far more riged than it was last week.
Re-positioned the duct as there was too much of a lip where it meets the hull
glued in the foam strip over the duct to be glassed for re-enforcement next week.
Foot plate mould given initial resin coat.
Forgot to charge my phone so no photos :facepalm:
Will either call in on thursday and get a few or get them off one of the other lads
|
Matty W
|
posted on 8th Mar 12 at 20:45 |
quote: Originally posted by Matt L
also... its an F3 :look:
Its actually an F2/FS now. since he decided to put the rotax in its going to be too powerfull to compete in F3. he stickered it up first then came across the engine and got a bit giddy
|
Matt L
|
posted on 8th Mar 12 at 20:03 |
now that looks :cool:
also... its an F3 :look:
|
Matty W
|
posted on 7th Mar 12 at 12:45 |
Cheers. well the choice in the club was formula ford, karting, engines or composites. as you'd expect the other groups filled up so its about 15 people stood around a single seater from the 70's and a group of about 7 working on an xe engine so i chose to do something a bit diffrent. expected completion around september time.
|
Gary
|
posted on 7th Mar 12 at 11:27 |
How has this gone un-noticed :!
Very Cool, dont see stuff like this about :cool:
|
Matty W
|
posted on 6th Mar 12 at 23:07 |
Small update:
Havent done much work to the craft for the past few weeks due to fabricating other parts for venom customers aswell as making parts for the Juno racecar ( one of the lecturers owns Juno racing )
We have all the moulds for the juno parts as it was designed at the uni
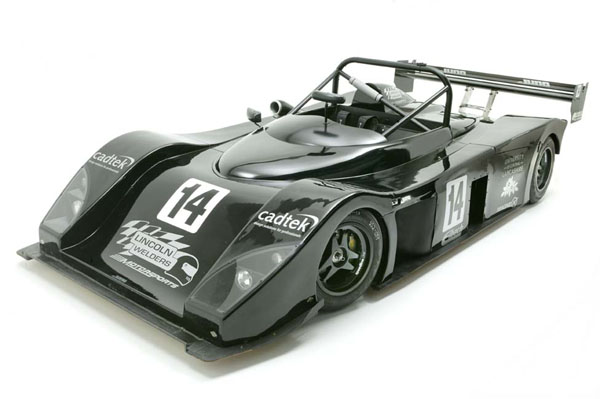
but back to the craft. the fibreglass rudders and flow straightners have now been made and cracked out of the moulds ready for fitting at a later date. the floor section has been made up a few weeks ago and today we got round to fitting that.
the floor section sits underneath the hull and is filled with air when the hovercraft is running. around the floor there are a number of holes (not yet drilled) that channel this air out into the skirt. this craft will run what is known as a finger skirt which is devided into 50+ sections. each finger covers one of the inlet holes. The advantage of a finger skirt to a bag skirt is that if one part of the skirt gets damaged, there will still be enough lift from the others. Finger skirts also take corners much better than bag skirt craft, but tend to plough in more on the front end in water, increasing drag.
floor under the hull
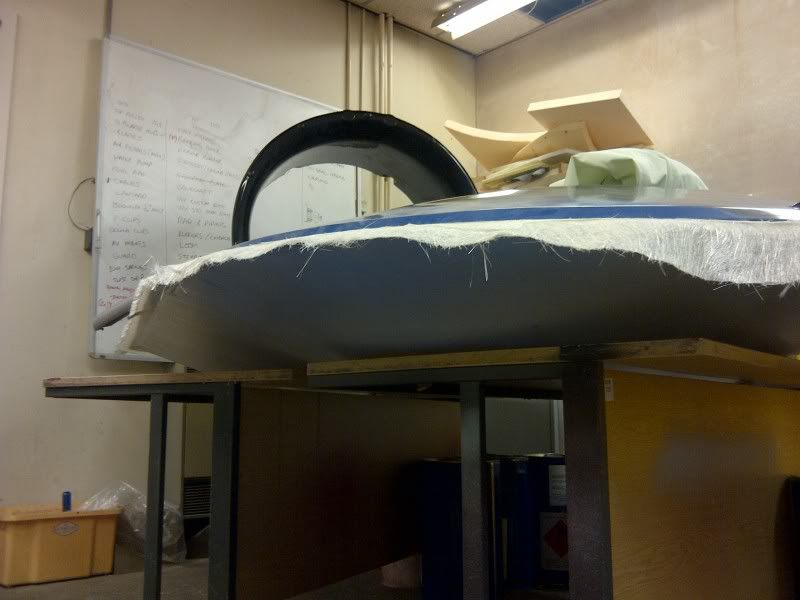
Clamped into place for cutting
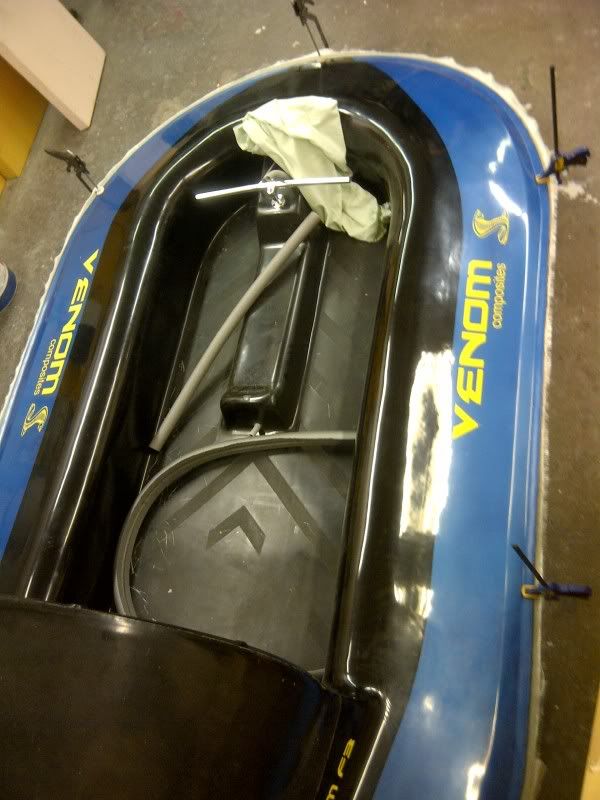
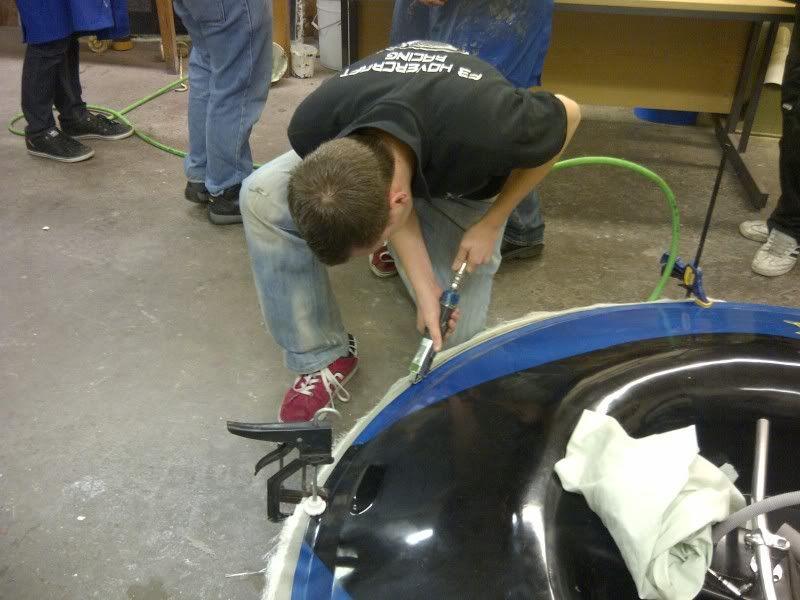
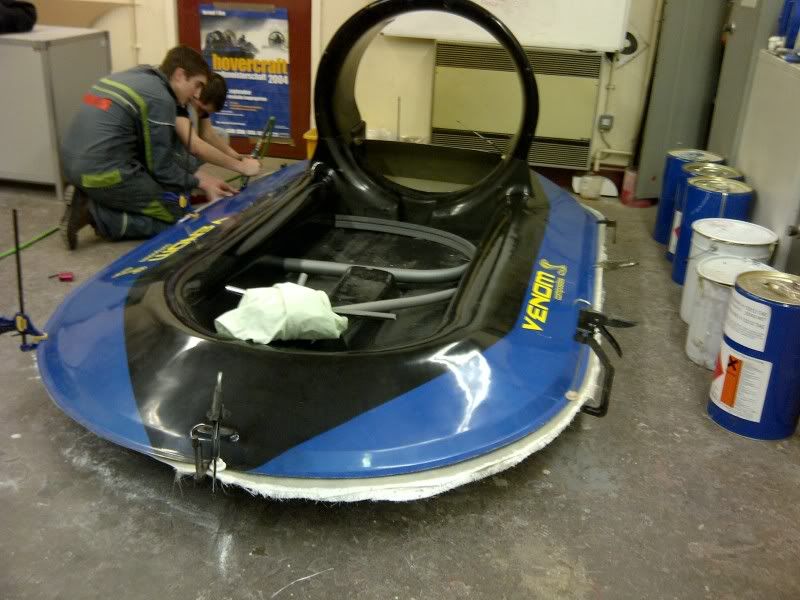
Alluminium edging the drilled and held into place with pannel clips and rivets
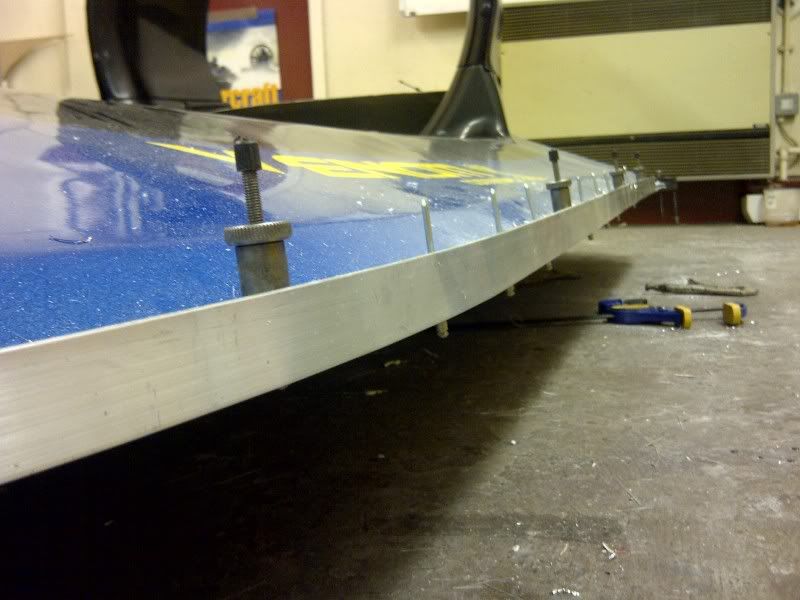
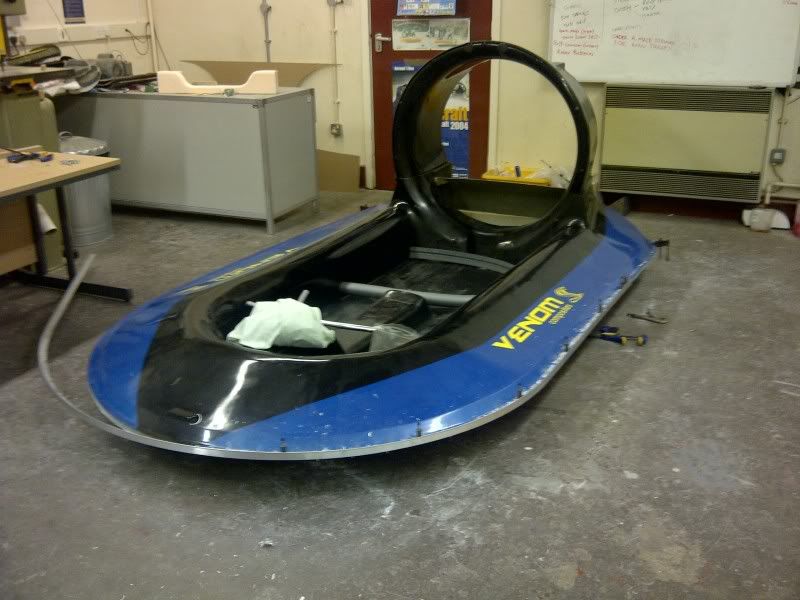
and the finished result
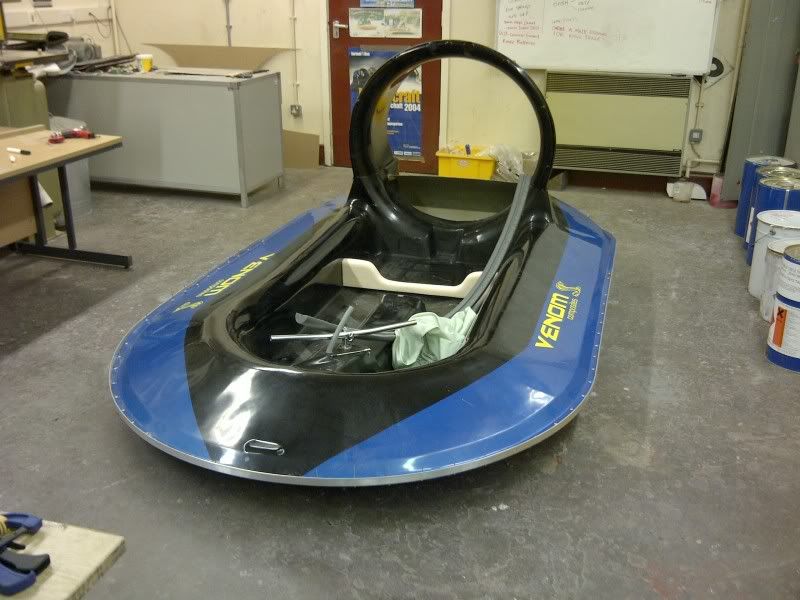
The alluminium edge increases the rigidity of the craft massively and is also where the skirt will be attatched to.
Saftey is a priority though :rolleyes:
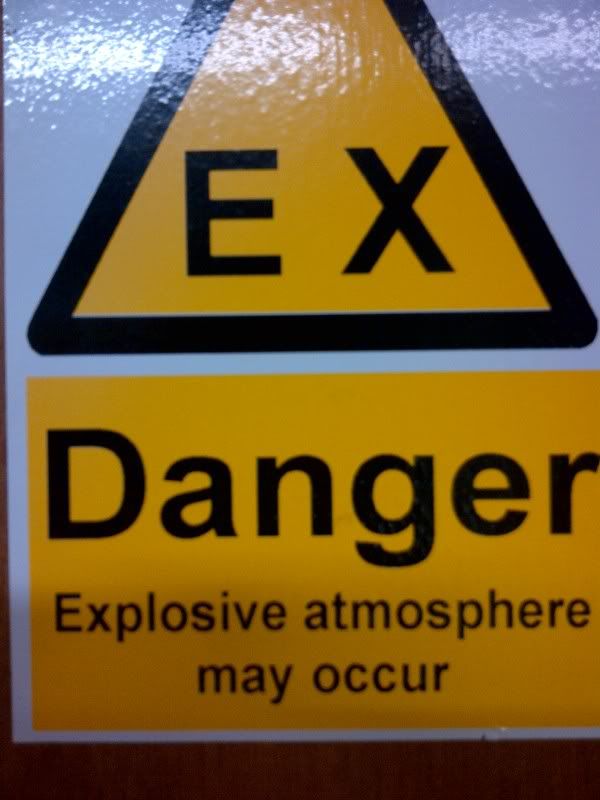
and this is one of the lads helping build the craft... he really likes monster
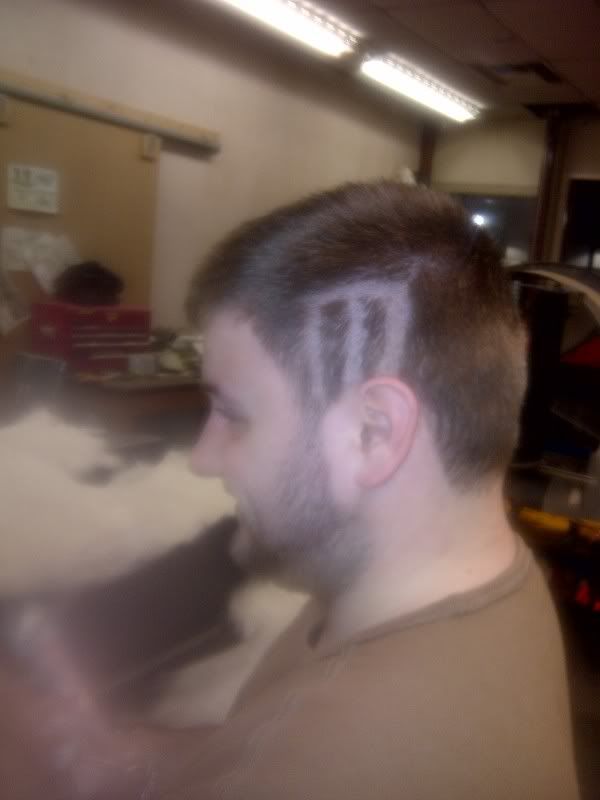
[Edited on 13-03-2012 by Matty W]
|
Matty W
|
posted on 7th Feb 12 at 22:26 |
My second build thread and its still not a corsa.
Im currently in my foundation year at uclan in preston studying Motorsport Engineering.
tuesday evenings is motorsport club which is basically access to the whole engineering workshop for the evening to do pretty much whatever you like, aslong as its related to motorsport. the main workshop contains 3 formula ford race cars maintained by students and raced for real at oulton and angelsey. theres an engine dyno test bay, with mapping software. gearbox workshop, and finally where ive been spending most of my time the past few weeks, the composites room.
ive come to this project at mid point as i was trying to decide on which activity to stick with, but the hovercraft seemed far too interesting to pass up.
the project is being run by Tony Broad, who races in formula 3 around the uk and europe. He was once one of the experts for scrap heap challenge on the airboat episode. He operates part of his company, Venom Composites from inside the uni, and builds craft to order letting students do alot of the work.
When i came to the project, the top body panell had been made and another student had just finished the steering set up and was prepairing the boyancy which is just big polystyrene blocks secured to the hull with expandy foam and carbon fibre. since then i have helped to fit the steering cable and rear duct, made some carbon fibre and kevlar end plates for the rudders and calculated the tuned length for the exhaust.
The finished craft will weigh about 125Kg and will be powered by a 110HP 2 stroke Rotax 493 engine from a snowmobile, making it pretty quick.
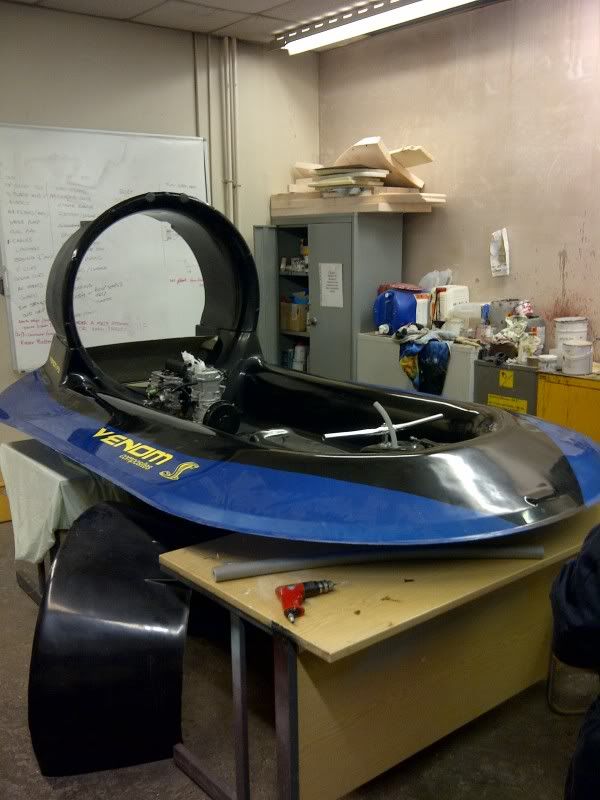
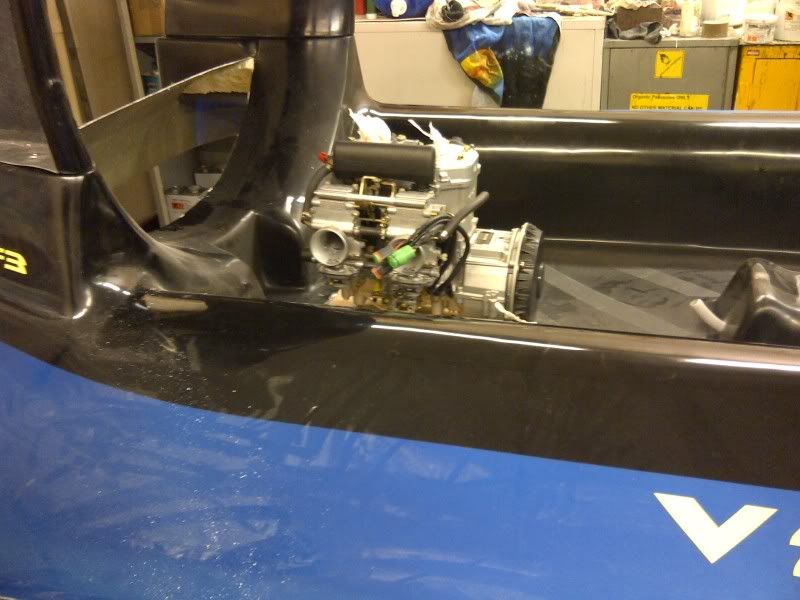
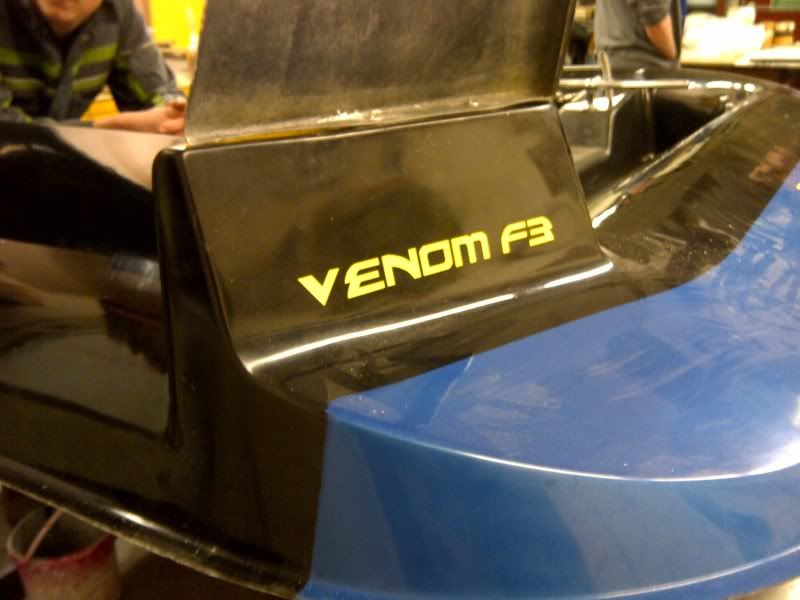
today was the task of cutting carbon fibre and kevlar ( not as easy as you might think ) to layer up into the end plates. forgot to take a pic as i was too busy trying to cut kevlar with a blunt blade, but heres one in the vac bag. The carbon and kevlar are pre-pregnated with resin, and when baked under vacuum they set
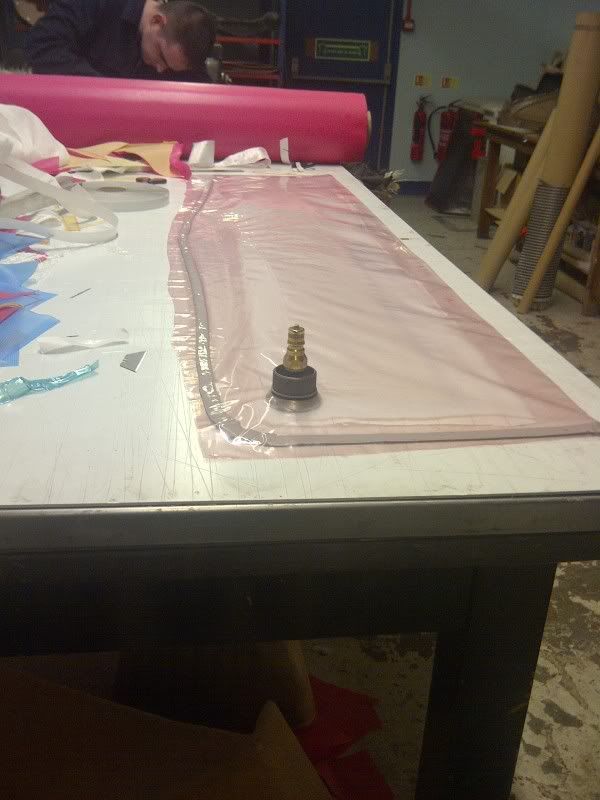
and with the off cuts i started making Mike a superlight keyring for the Corsa Superlaggera
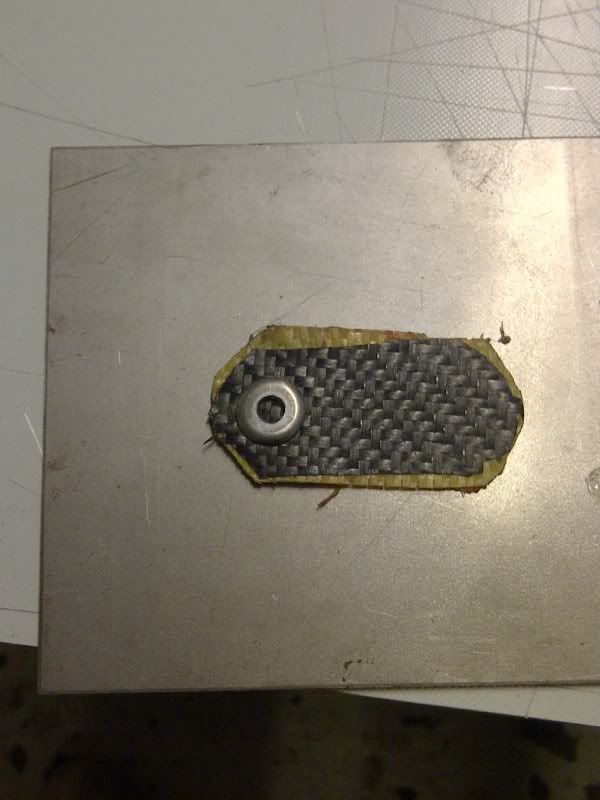
only rough but will be rounded off when its baked
[Edited on 13-03-2012 by Matty W]
[Edited on 29-04-2012 by Matty W]
|