|
jamesy1990
|
posted on 5th Aug 09 at 20:40 |
Am gona have to find some of these duraseals !!!!:thumbs:
|
Ian
|
posted on 5th Aug 09 at 20:34 |
Just solder them.
|
WATSON
|
posted on 5th Aug 09 at 19:21 |
I wouldnt twis and tape anything when it comes to electrical stuff, Can pick up an iron much cheapness or you can heat shrink.
|
SVM 286
|
posted on 5th Aug 09 at 19:15 |
Volkswagen AG style.
|
Kano
|
posted on 4th Aug 09 at 18:05 |
I've used those connectors hundreds of times and never realised they were able to be heat shrunk.. lol
|
moka
|
posted on 4th Aug 09 at 16:57 |
Superb mate thanks alot :thumbs:
[Edited on 04-08-2009 by moka]
|
Ste L
|
posted on 4th Aug 09 at 16:18 |
[QUOTE=nova-andy;3548332]Hi,
i dont know if this is the best place to post this??? Mods: can you move as approtiate please,
I have seen a lot of discussions around forums about the best way to join cabals in car looms this is my view on the best way,
I have heard many answers to this question which include:
Soldered and heat shrunk : This is generally seen as the “best” Method in many peoples eye’s, but IMHA (and work mates) can be one of the worst in a car loom situation, the main problem is soldering will produce a hard spot in the cable which unsupported will fracture and brake under vibration of a car. The over main problem with soldering is its not easy, I have been a apprentice wireman for 4 years now and my soldering is nowhere near the standard of some of “older generations” of work mates.
Twisted and tape/ heat shrunk: believe it or not this method is not as bad as people think, providing it is done properly. The RAF used twisted wires for many years in aircraft, as the wire is still flexible it is much less likely to brake under vibration
Crimped using bullets ECT: again this method is not that bad if done properly, using the correct crimp for the wire size and the correct tools is a must. The big down side to these is they can take up a lot of room as there bulky and thick.
So which is the best way to join a cable? Well none of the above, I use a special kind of crimp called “Duraseals”, they come in all type's and size's of crimps I.E. spade, splices, ring, ECT.
In breath the cable is crimped in the traditional manner (using the PIDG type crimp tool) and then the built in sleeving is heated which then shrinks around the cable insulation. Special adhesive flows during the heating to seal the joint. I have used thousands of them and have never had ONE fail.
You can find them in places like R.S, Farnell's and Maplins.
I will concentrate on splices in this how to but the over forums of the Duraseals you can use in the same way.
Tools you will need:
Crimp tool
Wire strippers
Hot air gun
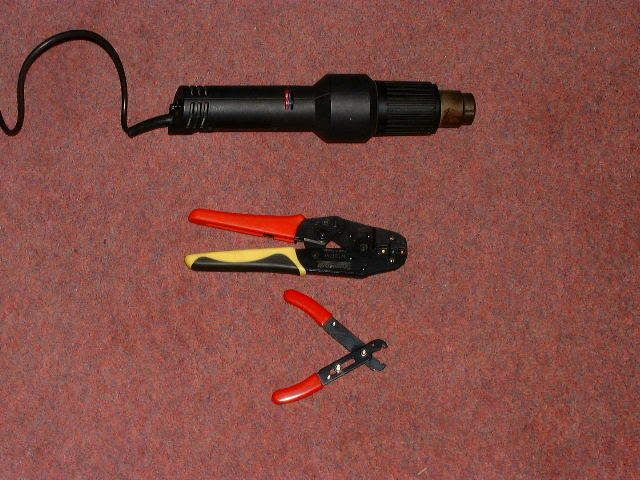
Step 1
The first step is to select the correct crimp size for the job, they come in 3 different sizes, RED: 0.5mm to 1.5mml, BLUE: 1.04mm to 2.63mm and YELLOW: 2.63mm to 6.64mm
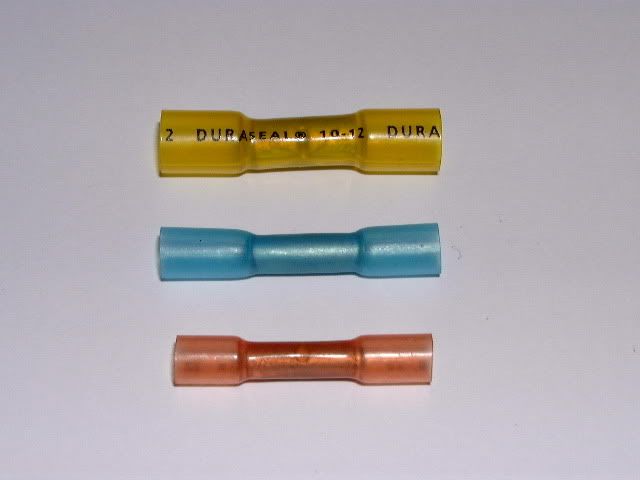
Step 2
Bear back the end of the cable using wire strippers taking care not to cut though any strands of the inner cable. For RED and BLUE you need to bear back 7mm and 5mm for yellow, I will be using RED in this demo,
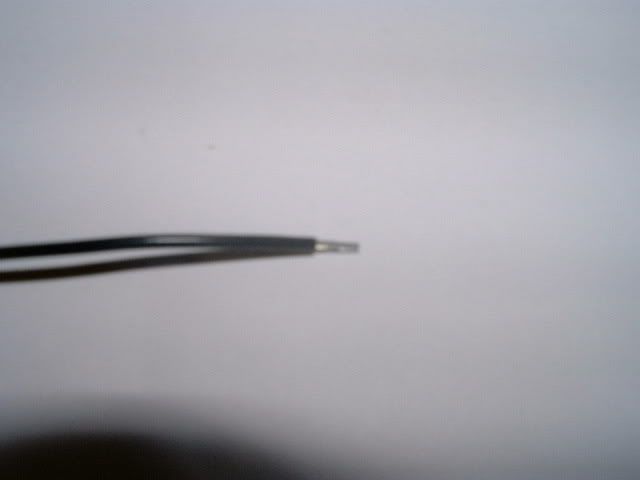
Step 3
Line up your crimp tool with your crimp and lightly crimp down just to hold the crimp in position make shore the jaws wont past the centre of the crimp, insert the cable and complete the crimp. Give the wire a good tug to make shore you have a good crimp

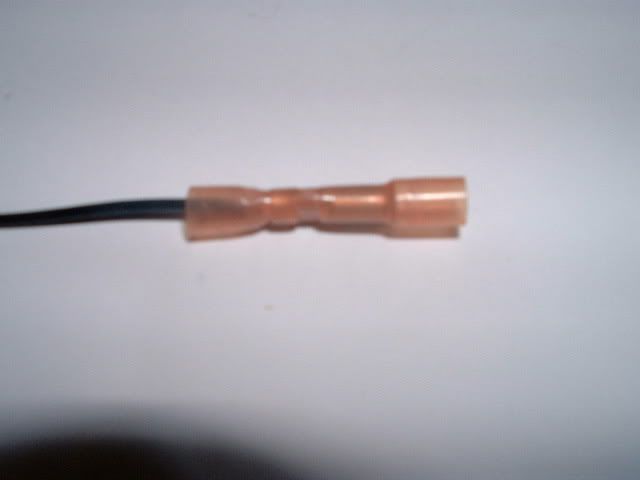
Step 4
Repeat for the over side.
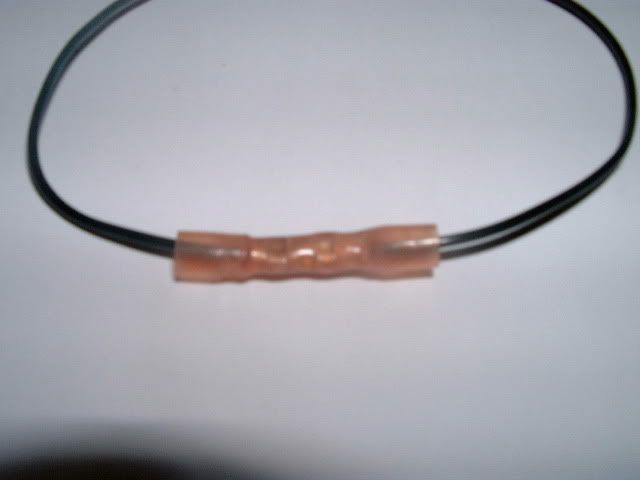
Step 5
Heat up the crimp with your hot air gun until it has fully shrunk and the glue comes out the end.
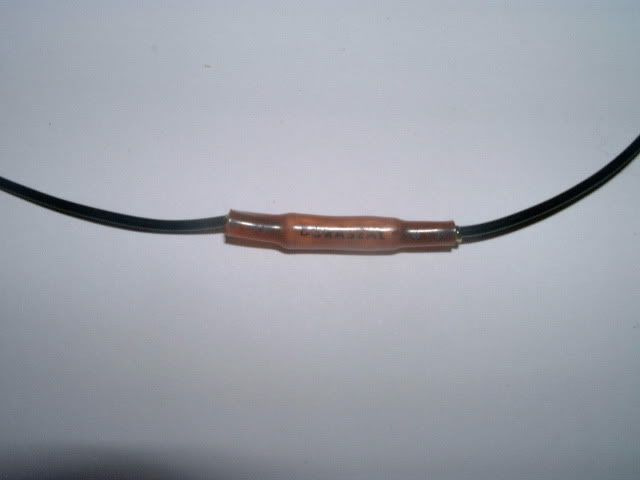
Step 6
That’s it your done! It’s that simple
You can also make “Y” leads with the splices
First strip back the two cables to be joined at least 10mm
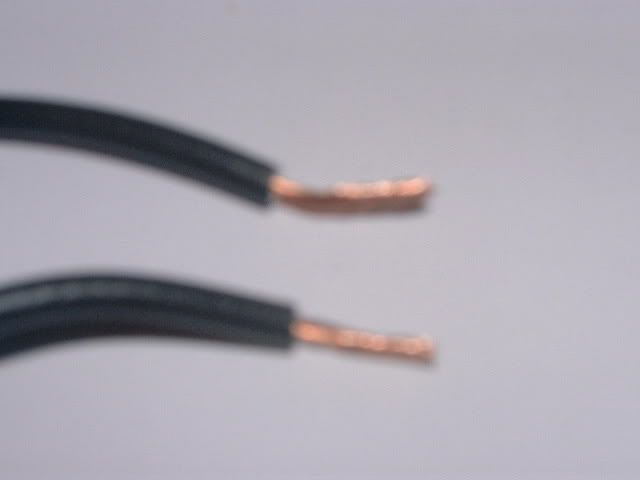
Twist them together and trim them off to the correct size (7mm or 5mm)
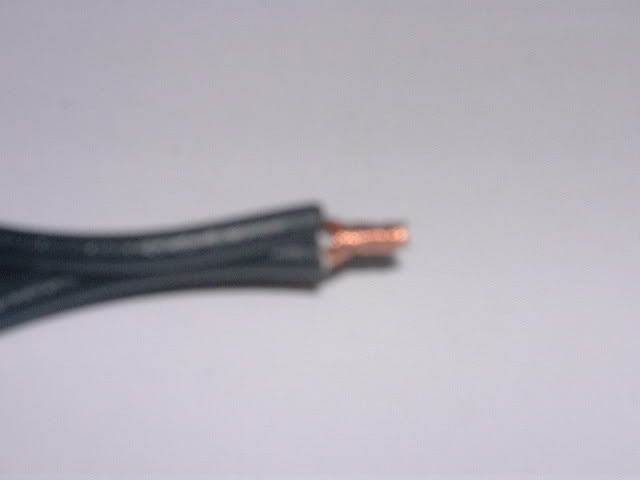
Repeat steps 3 to 5.
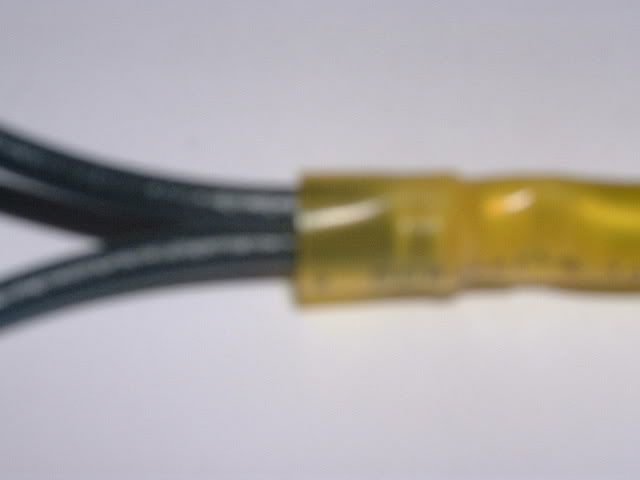
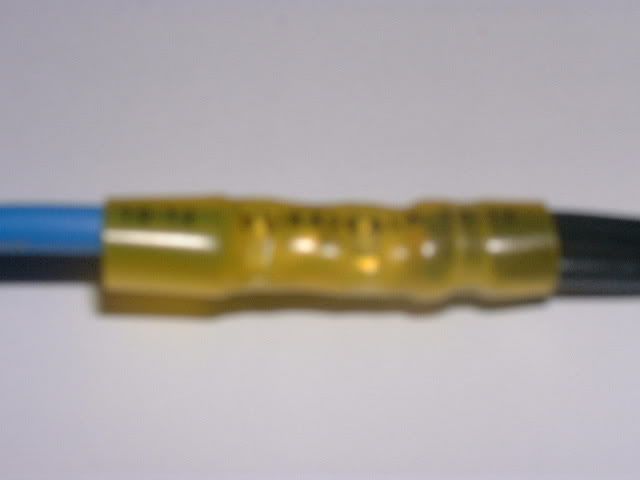
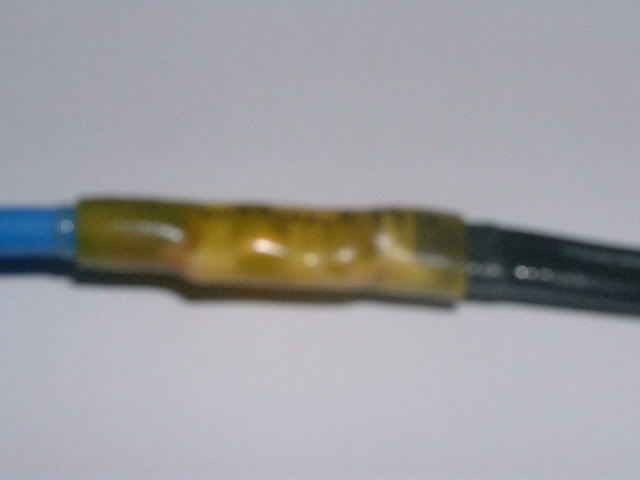
I hope this guide will be of help to people,
Happy wiring
Andrew Chilcott[/QUOTE]
|
Kurt
|
posted on 4th Aug 09 at 15:12 |
Scotch locks? :o
|
Shane
|
posted on 4th Aug 09 at 15:08 |
quote: Originally posted by DaveyLC
Buy a soldering iron you cheap bastid!
Or if getting mains power out to the car is a problem get a ColdHeat battery iron.
there about £4 in maplins and thats the cheapest ive found
|
DaveyLC
|
posted on 4th Aug 09 at 14:02 |
Buy a soldering iron you cheap bastid!
Or if getting mains power out to the car is a problem get a ColdHeat battery iron.
|
SVM 286
|
posted on 4th Aug 09 at 14:00 |
Purchase a soldering iron. :)
|
deano87
|
posted on 3rd Aug 09 at 06:21 |
Spade or bullet connectors and crimping tool.
|
craigpcg
|
posted on 2nd Aug 09 at 23:39 |
If you use a proper crimping tool ie not a pair of pliers then they wont crush the wires :D
|
Richardhhha
|
posted on 2nd Aug 09 at 23:36 |
only ting with crimps is that is that it crushes the wiring causing it to become week, low temp solder srink wraps are best way imop
|
craigpcg
|
posted on 2nd Aug 09 at 23:12 |
connector block is rubbish.
I personally use crimps which u can buy from any diy shops ie b&q (other oulets are avaliable) lol
|
inliner04
|
posted on 2nd Aug 09 at 22:59 |
connector block. . .
|
Richardhhha
|
posted on 2nd Aug 09 at 22:49 |
http://www.calcentron.com/Pages/fusion_solder_heat_shrink/fusion_solder_heat_shrink.html
|
moka
|
posted on 2nd Aug 09 at 22:48 |
I normally just twist and tape?
|
moka
|
posted on 2nd Aug 09 at 22:45 |
Best way to repair electrical connections without soldering?
Reason i ask in here is because its in the car!
Recently fitted amp, was told to solder but i have no soldering iron. Also fitted a different light and didnt solder.
|